Building Thermograpy
Background
Building inspection is a fast-growing application of infrared thermography, which can be used to test and solve problems in buildings of any age, size, use or construction type. The key benefits are that it allows non-destructive and non-contact assessment of the structure’s and/or location and size of defects within building structures, components or systems to be carried out. With suitable equipment, large areas of buildings can be scanned and assessed in a relatively short time.
Thermography is still an emerging technology across the construction industry, with growing levels of awareness and an ever-increasing number of applications, but relatively little real understanding of what it can and cannot provide, and how and when to use it effectively. One of the most important factors with thermal imaging of buildings is consideration of weather and environmental conditions, which can in many cases be critical to successful use.
Architects, builders, facility managers, surveyors, loss adjusters and many other building professionals, as well as individual home owners, can benefit from thermal imaging surveys. The key uses are summarised below.
Building Fabric heat loss
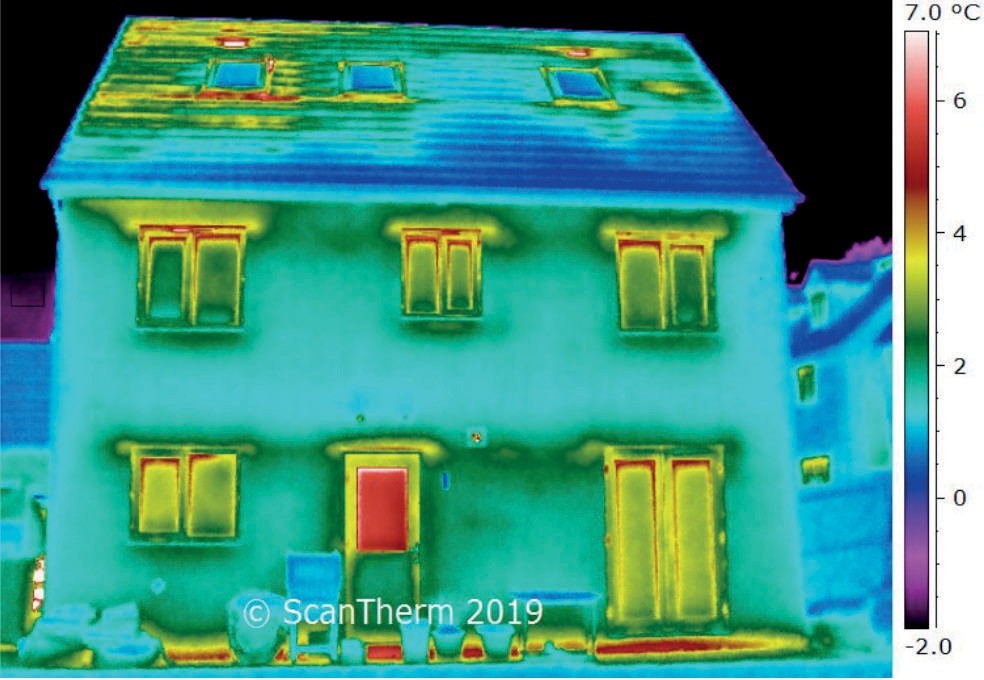
Figure 1. Heat loss – external image
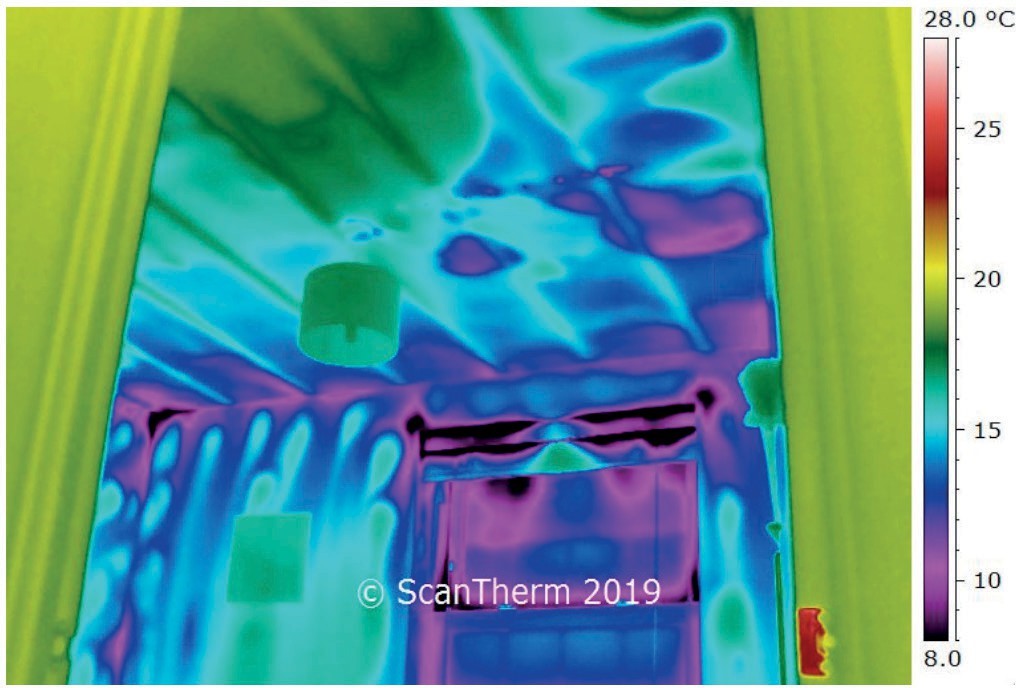
Figure 2. Heat loss using blower door – internal image
One of the best known uses for building thermography is to assess thermal insulation (as required by Part L of UK Building Regulations) and other key sources of heat loss such as thermal bridging and excessive air infiltration around the building fabric. It can be very useful to use a ‘blower door’ (used to test the air tightness of buildings) together with thermal imaging to locate the sources of draughts and interstitial air movement.
The weather and environmental conditions are critical for heat loss surveys; a cold and dry morning is generally required, prior to sunlight warming the building, so inspection typically can take place between September and May in the UK. Wherever possible, internal scans should be performed to fully understand heat loss and its likely mechanisms.
A great deal of caution should be applied where external-only scans are recommended, since, in many cases, the location of external ‘hot spots’ may not necessarily identify the corresponding internal ‘cold spot’. Surveys incorporating both internal and external thermal imaging are of course more time consuming and complex but, in general, only a basic impression of a building’s thermal performance can be determined from an external survey.
Structural damp and leak tracing
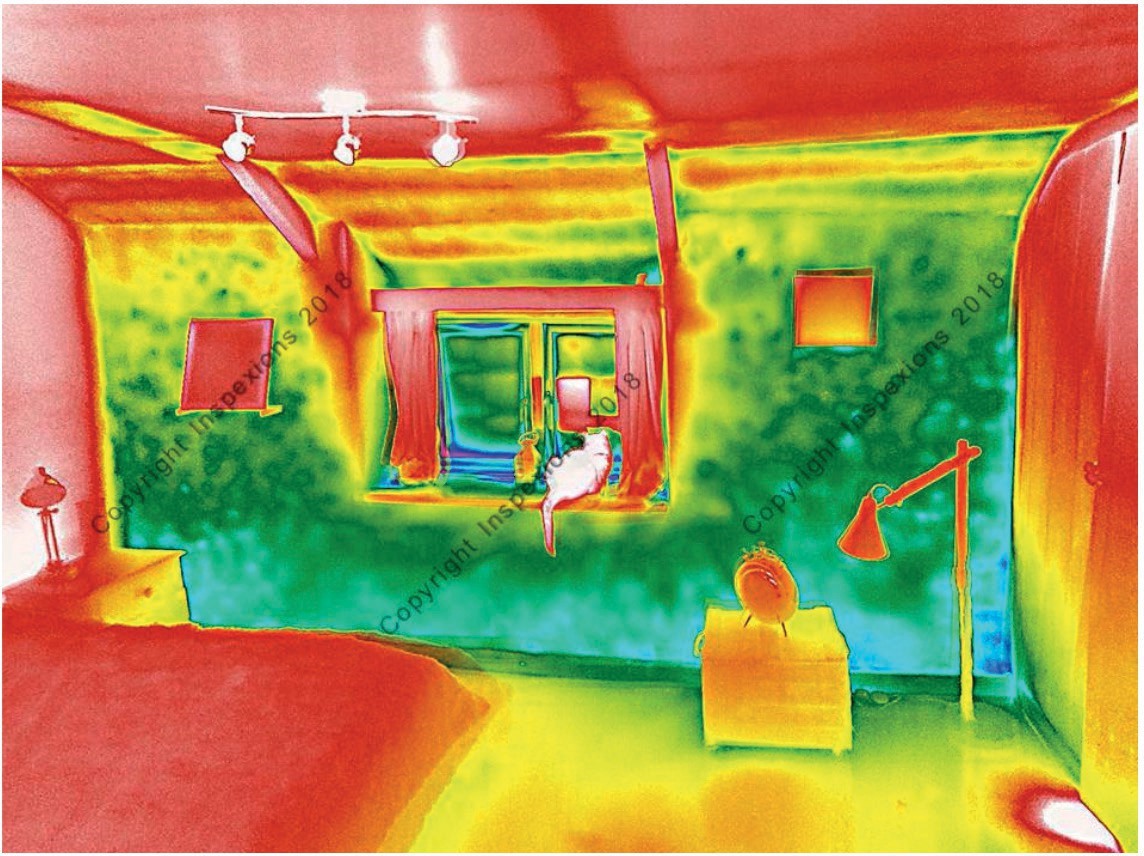
Figure 3. Damp survey showing moisture in lower wall
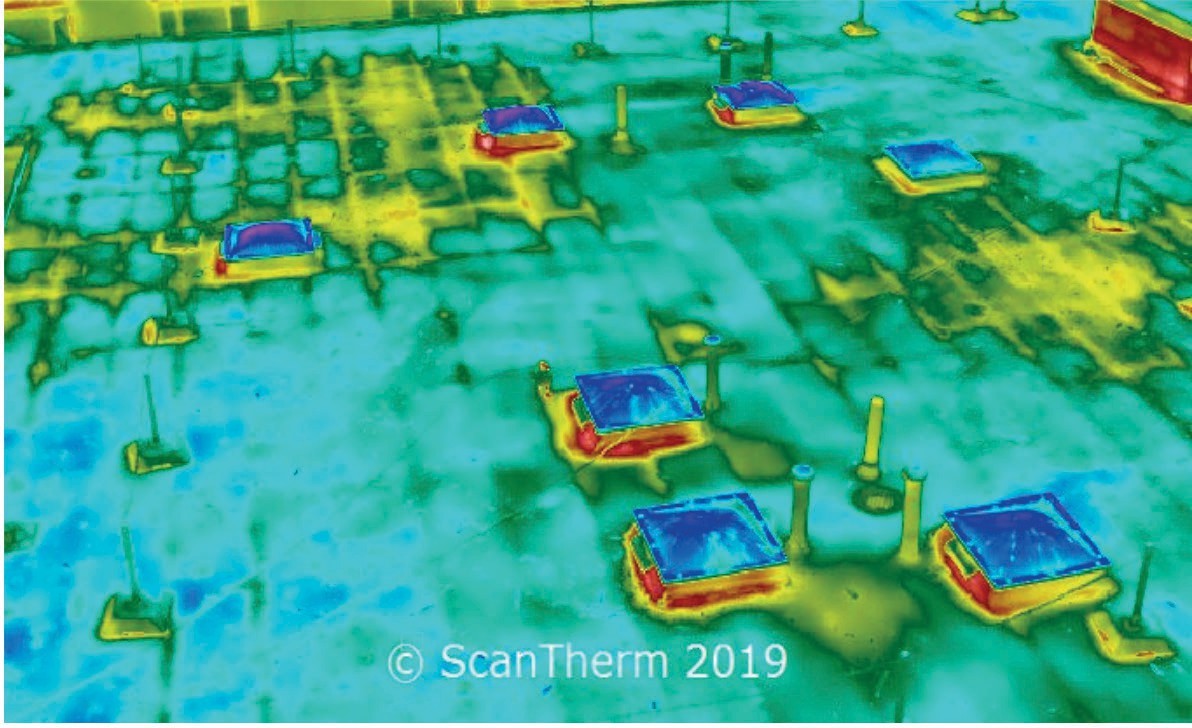
Figure 4. Roof survey showing water-damaged insulation
Structural damp and leak tracing is very valuable for building owners, managers and many construction professionals. Thermal imaging provides non-destructive investigation to locate areas that are damp and often enables the sources of damp to be identified, whether they be in the roof, walls, floors, windows or doors.
Additional specialised equipment is often required to assist in this process and verify suspected damp. Depending on the particular situation, the weather conditions may be important and should be considered by the thermographer.
Building services
Plumbing, heating and ventilation systems can be tested for performance, location (for example the precise position of under floor heating systems) or leaks. Generally, these surveys are not weather dependent.
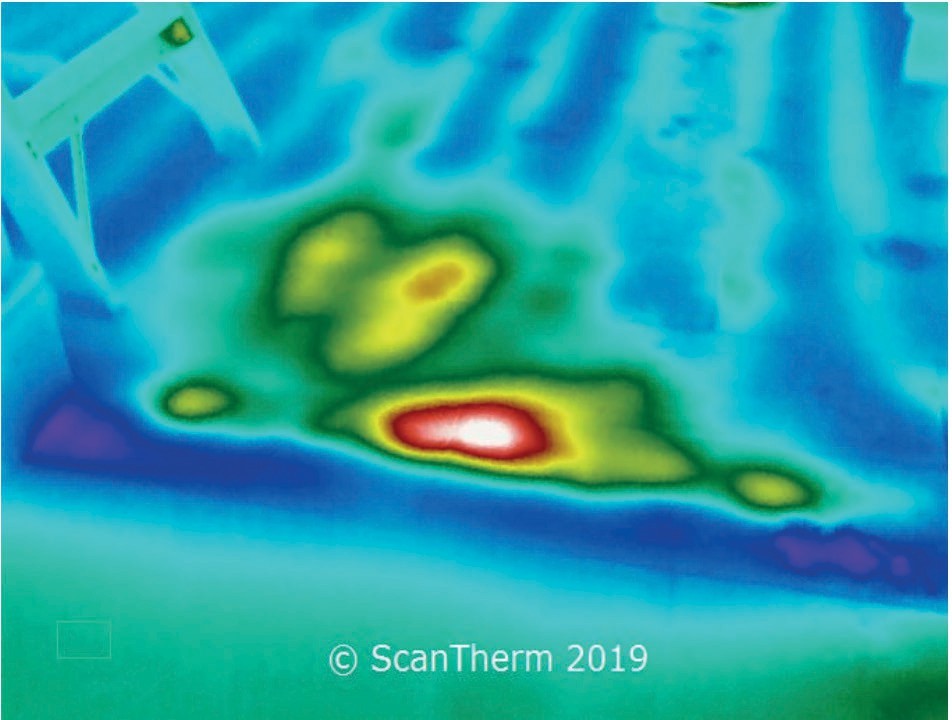
Figure 5. Underfloor heating system leak
What competencies should clients look for?
To fully realise the benefits of building thermography, it is essential that personnel are suitably trained/experienced and use suitably specified thermal imaging cameras and ancillary equipment. In addition to being trained and experienced in thermal imaging technology, knowledge of construction methods and building physics are equally important.
As many thermographic building surveys are conducted on live construction sites, suitable health & safety (H&S) training and certification may be required, such as possession of a Construction Skills Certification Scheme (CSCS) card or relevant accreditation by one of the construction H&S programmes.
It is often said that, with building thermography, the ‘devil is in the detail’. This applies to the planning of a survey (weather forecast, construction details, access and so on), as well as the survey itself and subsequent analysis and reporting. A competent building thermographer will almost always ask lots of questions, drilling down into what is required and then suggesting and explaining methods required to achieve it. Clients should expect this and ask plenty of questions themselves.
The UKTA suggests that, for accuracy and quality of content, survey reports are completed by personnel who have completed appropriate thermography training. Although this does not guarantee competence, it will at least mean that the knowledge and experience of personnel will have been assessed to a standard that aims to ensure that inspections are completed in a safe manner while realising the benefits of building thermography for the client.
Due to the size of buildings and, in many cases, the small temperature differences and subtle patterns being studied, most building thermography requires the use of a mid- to high-specification thermal imaging camera. While locating a hot pipe in a floor can sometimes be achieved with one of the increasingly available low-cost cameras, conducting a whole building survey requires equipment of a much higher specification. The UKTA looks to best practice and recommends that members use, as a minimum specification, a camera containing a 320 × 240 pixel detector. For thermographic surveys of larger/commercial buildings, or where improved image detail is required, the UKTA recommends cameras with a higher pixel count (640 × 480 or 1024 × 786) and superior thermal resolution (40 mK or better).
BREEAM
The BREEAM (Building Research Establishment Environmental Assessment Methodology), for both new build and refurbishment projects, is structured to analyse, rate and certify a building’s environmental and sustainability characteristics. A thermographic survey carried out at completion of the building can contribute towards BREEAM ratings. However, surveys must be conducted by a thermographer with a certification at Level 2 (or equivalent) or higher in accordance with ISO 18436-7. It is the commissioning organisations responsibility to check the thermographer chosen is suitably qualified as a copy of the qualifications must be submitted to the BREEAM Assessor to be awarded the relevant marks.